Common Implementations of Chemical Defoamer Across Various Sectors
Common Implementations of Chemical Defoamer Across Various Sectors
Blog Article
Exploring the Conveniences of a Chemical Defoamer in Manufacturing and Production
The assimilation of chemical defoamers in manufacturing and production procedures offers a tactical advantage by attending to one of the relentless obstacles in industrial procedures: foam control. As suppliers strive to optimize processes and enhance customer satisfaction, the function of chemical defoamers comes to be significantly essential.
Relevance of Foam Control
While the visibility of foam in making procedures can in some cases appear safe, effective foam control is important for optimizing operational efficiency and item quality. Foam can disrupt different stages of production, leading to inadequacies that may prolong and raise prices handling times. In sectors such as food and drink, pharmaceuticals, and chemicals, uncontrolled foam can obstruct devices, interfere with automated systems, and inevitably lead to product variances.
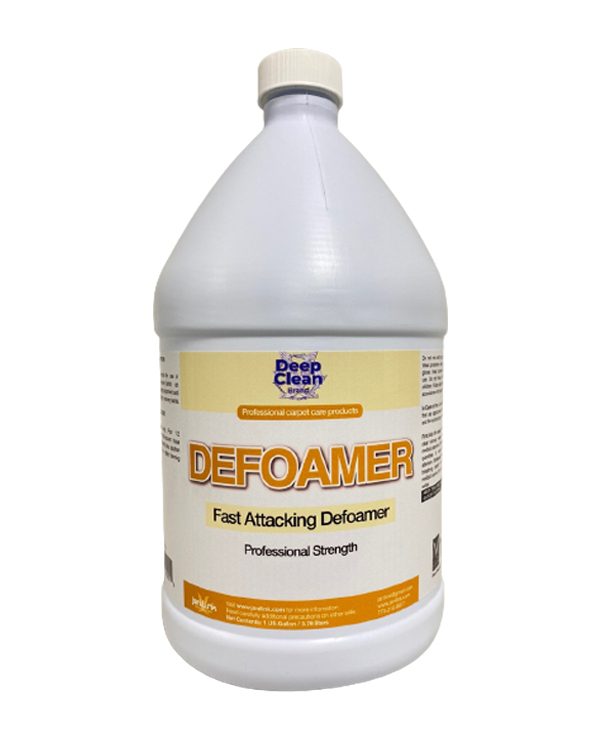
Applying reliable foam control strategies not only enhances productivity however additionally supports governing conformity in sectors where foam can result in environmental issues. By using chemical defoamers, makers can minimize these obstacles, making certain smoother procedures and higher-quality end items. Inevitably, focusing on foam control is an essential aspect of manufacturing that can produce substantial advantages in terms of effectiveness, security, and product integrity.
Kinds Of Chemical Defoamers
What types of chemical defoamers are available for manufacturing procedures, and just how do they vary in application? Chemical defoamers can be categorized into 3 primary types: silicone-based, organic, and not natural defoamers. - Chemical Defoamer
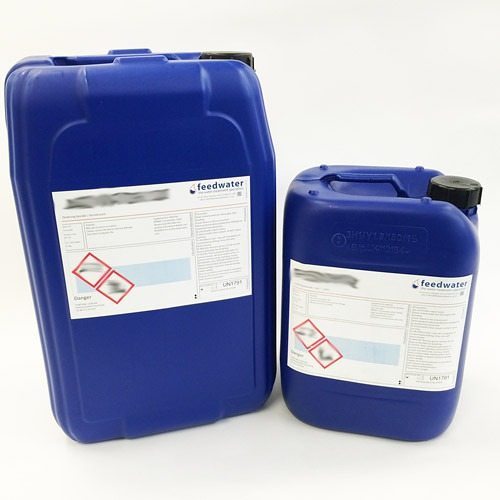
Organic defoamers, typically stemmed from fatty acids or all-natural oils, work in a variety of applications, consisting of food and beverage manufacturing. They are typically favored for their lower toxicity and ecological effect, making certain conformity with market guidelines.

Each kind of defoamer offers distinct objectives based on the chemical make-up and the certain requirements of the production process, permitting makers to choose one of the most suitable alternative for their specific demands.
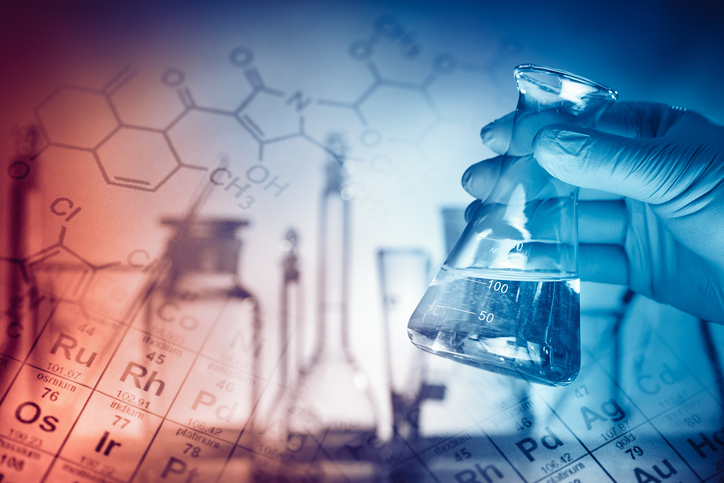
Benefits in Manufacturing Performance
Chemical defoamers play an important duty in improving making efficiency by successfully controlling foam generation throughout numerous processes. Foam can impede manufacturing rates, interrupt tools operation, and cause costly downtime. By integrating chemical defoamers, makers can minimize these issues, making sure smoother operations and increased overall efficiency.
Using chemical defoamers assists optimize the operational performance of equipment such as pumps, mixers, and reactors. With reduced foam, these equipments can operate at their meant capability, decreasing the risk of overflow and allowing constant handling. This results in much better source use and greater throughput.
Moreover, chemical defoamers facilitate faster processing times by reducing the time required for foam Recommended Site elimination. This velocity can substantially influence manufacturing timetables, allowing manufacturers to meet consumer need a lot more properly. In addition, using defoamers adds to decrease power intake, as equipment runs extra successfully with lowered foam disturbance.
Influence On Item High Quality
Foam control is not just necessary for preserving effectiveness in producing processes but also plays a significant role in making certain item top quality. Extreme foam can introduce air into formulations, bring about incongruities in the last item. This can materialize as problems such as voids, irregular appearances, or below average surfaces, which undermine the desired top quality and performance of the product.
Moreover, foam can hinder the homogeneity of combinations, leading to unequal distribution of energetic ingredients. In industries such as coverings, cosmetics, and food manufacturing, this can lead to variations in shade, taste, and general effectiveness. By utilizing a chemical defoamer, manufacturers can reduce these dangers, guaranteeing that items satisfy rigid quality requirements.
In addition, managing foam can enhance the security of emulsions and suspensions, which is important for ensuring shelf-life and customer fulfillment. With enhanced item consistency and reduced flaws, producers can attain higher criteria of quality control, ultimately causing increased consumer depend on and brand loyalty.
Cost-Effectiveness and ROI
Efficient foam control not only improves item quality Bonuses however likewise adds substantially to the total cost-effectiveness of manufacturing processes. Making use of chemical defoamers decreases foam-related issues, which can otherwise cause manufacturing hold-ups, equipment malfunctions, and raised energy usage. By lowering foam, manufacturers can enhance their procedures, leading to higher throughput and effectiveness.
Buying chemical defoamers can yield a considerable roi (ROI) The initial costs associated with these additives are frequently offset by the cost savings understood from lowered downtime and improved material return. Boosted item top quality can reduce waste and rework prices, additionally boosting financial performance.
Additionally, effective foam control can result in decreased water and energy usage, contributing to lower operational costs. This is particularly important in industries where resource efficiency browse around this site is paramount. By integrating chemical defoamers into their processes, manufacturers can attain lasting financial savings while keeping affordable prices in the market.
Final Thought
In verdict, the combination of chemical defoamers in production and manufacturing processes is crucial for enhancing functional efficiency and improving item high quality. The benefits provided by chemical defoamers not only support governing compliance yet likewise offer an affordable edge in the production landscape.
The combination of chemical defoamers in production and manufacturing procedures supplies a tactical benefit by dealing with one of the relentless difficulties in industrial operations: foam control.While the presence of foam in producing procedures can sometimes seem harmless, effective foam control is vital for maximizing operational performance and product high quality.Chemical defoamers play an important duty in improving manufacturing effectiveness by effectively managing foam generation throughout different procedures.Moreover, chemical defoamers assist in faster handling times by decreasing the time needed for foam elimination. Additionally, the usage of defoamers adds to lower energy usage, as equipment operates a lot more successfully with lowered foam interference.
Report this page